When designing a modern cleanroom, much of the attention is focused on elements like filtration systems, flooring, and walls. However, choosing the right cleanroom furniture is equally critical to maintaining the pristine environment needed for contamination control. Properly selected cleanroom furniture and accessories not only ensure compliance with cleanliness standards but also contribute to workflow efficiency and operator comfort. In this expanded guide, we will cover the key aspects of selecting the best cleanroom furniture and supplies to meet your specific needs.
Why Cleanroom Furniture Matters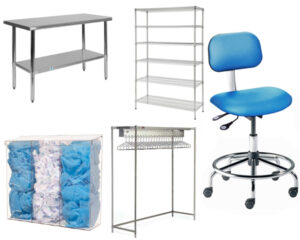
The role of cleanroom furniture goes beyond providing functional surfaces or seating. In controlled environments, every piece of furniture can be a potential source of contamination if not selected with care. The materials, construction, and placement of each item play a role in maintaining the cleanliness of the space.
When setting up a pharmaceutical lab, electronics factory, or biotech research center, choose the right cleanroom furniture. This helps keep the area clean and supports the work done there.
Understanding Cleanroom Classification Standards
Cleanrooms are classified based on the number and size of particles permitted per volume of air. For example, an ISO Class 5 cleanroom allows fewer particles than an ISO Class 7 cleanroom. The classification directly impacts the type of cleanroom furniture required. In high-class cleanrooms, even minor particle emissions from surfaces, seating, or shelving can compromise the cleanliness of the environment.
Matching Furniture to Cleanroom Classifications
- ISO Class 1-5 Cleanrooms: In these high-class cleanrooms, furniture must be designed to release minimal or no particles. Stainless steel is a common material used for surfaces like tables and benches because it is non-porous, easy to clean, and does not harbor contaminants. Chairs for these environments often come with specialized filtration systems to capture microparticles.
- ISO Class 6-9 Cleanrooms: In lower-class cleanrooms, the furniture requirements may be less stringent, but it’s still essential to select materials that resist particle accumulation and are easy to sanitize. Plastic-coated surfaces, powder-coated steel, or chemical-resistant laminates may be suitable in these environments.
Common Types of Cleanroom Furniture
Each cleanroom setup varies based on the operations being conducted, but some pieces of furniture are universally common across cleanroom environments. These include tables, chairs, workstations, shelving, and storage solutions. Here’s a closer look at the most common types of cleanroom furniture:
Workbenches, Workstations, and Tables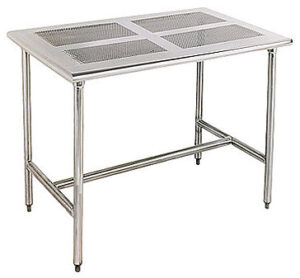
Tables and workbenches are a staple of any cleanroom environment. However, the selection of these items should be based on the type of activities that will occur. In cleanroom design, tables, workstations, and benches are often used interchangeably, but subtle differences make each one better suited to specific tasks.
- Workbenches: These are often customized for specific operations like assembly or testing. Workbenches in cleanrooms should be made from materials like stainless steel or chemical-resistant laminates to ensure cleanliness and durability. The surfaces should be easy to wipe down and smooth to prevent particle buildup.
- Workstations: Cleanroom workstations often include additional features like power outlets, shelving, or integrated sinks for cleaning equipment or hands. Workstations designed for electronics manufacturing may also include electrostatic discharge (ESD) protection.
- Tables: General-purpose tables in cleanrooms may be used for activities like packaging, inspection, or research. These tables should be modular or mobile to allow for flexibility in reconfiguration as needed.
Chairs for Cleanrooms
The right seating is essential for ensuring operator comfort and maintaining cleanroom standards. Cleanroom chairs are not like standard office chairs. They are designed with specialized filtration systems to prevent particle release. Chair classes:
- Class 10-100 Chairs: These chairs have built-in filters to capture particles as small as 0.3 microns. The chair is often sealed with vinyl or polypropylene to prevent particles from escaping, which is crucial for high-class cleanrooms where even minute contaminants can compromise the environment.
- Class 1,000-10,000 Chairs: While less stringent, these chairs still come with particle filtration systems. For optimal protection, using the same filter material as in Class 100 chairs can cover exhaust vents, further minimizing contamination risk.
Comfort is also a significant factor. Cleanroom operators may spend long periods seated, so ergonomic design is important. Adjustable height settings, back support, and smooth gliding wheels can enhance worker comfort and productivity.
Shelving and Storage Systems
Storage solutions in cleanrooms must balance organization with contamination control. Open shelving, closed cabinets, and modular storage systems all play roles in optimizing the workspace.
- Shelving Units: Stainless steel shelving is the most common option for cleanrooms because it is resistant to rust, corrosion, and contamination. Adjustable shelving allows for easy reconfiguration, which is particularly useful in modular cleanrooms or those that handle various processes.
- Cabinetry: Closed cabinets are ideal for storing sensitive materials or tools that must be kept sterile. Opt for cabinetry with smooth surfaces and minimal joints to prevent particle accumulation.
Key Considerations for Selecting Cleanroom Furniture
Choosing the right cleanroom furniture involves more than just selecting pieces that meet basic standards. Several factors need to be considered to ensure the furniture aligns with the specific requirements of your cleanroom environment.
1. Chemical and Material Resistance
Cleanrooms often use chemicals or processes that require specific surface treatments or materials. For example, if your cleanroom involves the use of caustic chemicals, you will need work surfaces that are resistant to corrosion or chemical damage. Similarly, operations that generate heat may require heat-resistant surfaces to avoid damage or contamination.
2. Layout and Workflow Optimization
The layout of your cleanroom plays a crucial role in workflow efficiency. Consider how many workstations, storage areas, and seating arrangements are necessary for optimal operations. For example, a cleanroom used for quality control testing might require multiple workstations with integrated power sources and sinks, while a cleanroom used for packaging may need tables and shelving units optimized for material handling.
3. Flexibility and Mobility
As processes evolve, so should your cleanroom’s furniture setup. Opt for modular furniture or pieces on wheels that can be moved and reconfigured as needed. Adjustable-height tables and mobile shelving units allow you to make quick changes without disrupting cleanliness or operations.
4. Cleanroom Supplies
In addition to furniture, cleanroom supplies are essential for maintaining a contamination-free environment. Adhesive sticky mats placed at entry points trap dirt and particles before they enter the room. These mats must be replaced regularly to maintain effectiveness.
Cleanroom vacuums and wipes are also critical tools in ensuring cleanliness. Regular cleaning of surfaces, floors, and equipment prevents the buildup of contaminants.
Setting Up Your Cleanroom Furniture for Success
Whether you are designing a new cleanroom or upgrading an existing one, the importance of selecting the best cleanroom furniture cannot be overstated. By choosing furniture that aligns with your cleanroom’s classification, chemical use, and workflow, you can ensure compliance with cleanliness standards while enhancing the efficiency of your operations.
At Modular Cleanrooms, we specialize in providing high-quality cleanroom furniture and supplies. Our team is here to help you select the right products tailored to your specific needs. Whether you require specialized workstations, seating, or storage solutions, we offer a wide range of customizable options.
If you need help selecting the best furniture or would like to request a quote, please fill out our contact form or give us a call today!