Cleanrooms are essential in controlled environment technology, and crucial for the development and research of chemicals, medicines, and other sensitive materials. At Modular Cleanrooms, we are industry experts in cleanroom design across the country, providing solutions tailored to meet each company’s specific requirements and building capabilities.
When building a cleanroom, choosing the appropriate structure is vital. Our team ensures that each project is executed with precision, utilizing the best materials for your specific application. The primary types we offer are hardwall and softwall cleanrooms, each with distinct features and benefits.
Softwall Cleanrooms
Features and Benefit
Softwall cleanrooms offer a portable enclosure in any size, making them highly adaptable to various needs. These are constructed using flexible vinyl curtains that provide an effective barrier for creating controlled environments.
- Portability and Flexibility: Softwall cleanrooms offer a portable enclosure in any size, making them highly adaptable to various needs. These are constructed using flexible vinyl curtains that provide an effective barrier for creating controlled environments.
- Material: The use of flexible vinyl curtains ensures versatility and ease of setup. The curtains can be easily adjusted or replaced, offering a cost-effective solution for temporary or changing needs.
- Purpose: Ideal for containing dust and sound, they provide a safe, enclosed space for numerous applications. They are particularly useful in situations where rapid deployment and adaptability are crucial.
- Ease of Construction: They can be quickly constructed and expanded, making them suitable for projects with tight timelines. This feature makes them an excellent choice for industries that require quick and efficient solutions.
- ISO Cleanliness Classifications: Available in a variety of ISO cleanliness classifications, they can meet different industry standards. They are suitable for industries such as electronics, pharmaceuticals, and biotechnology, where varying levels of cleanliness are required.
Limitations
- Cleaning: They can be harder to clean compared to their hardwall counterparts. The flexible vinyl material can accumulate dust and contaminants, requiring more frequent and meticulous cleaning.
- Static Pressure: These have lower static pressure, making them less suitable for applications requiring stringent particulate control. Industries that need higher levels of contamination control might find hardwall cleanrooms more appropriate.
- Chemical Resistance: These are not ideal for environments involving harsh chemicals. The flexible vinyl material can degrade when exposed to certain chemicals, reducing its longevity and effectiveness.
Hardwall Cleanrooms
Features and Benefits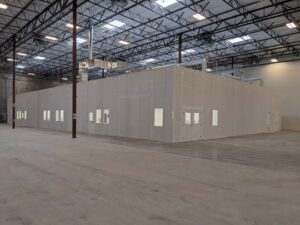
Hardwall cleanrooms provide a stable and secure environment, ideal for critical applications requiring stringent control over contaminants. The rigid structure ensures that it maintains its integrity over time, offering a reliable solution for long-term projects.
- Stability and Security: Hardwall cleanrooms provide a stable and secure environment, ideal for critical applications requiring stringent control over contaminants. The rigid structure ensures that it maintains its integrity over time, offering a reliable solution for long-term projects.
- Material: Made with prefabricated, demountable wall systems, they are designed for durability and easy assembly. The solid walls offer superior protection against contaminants, ensuring a high level of cleanliness.
- Purpose: These offer the highest level of control, effectively keeping airborne contaminants out and maintaining a pristine environment. They are perfect for industries such as pharmaceuticals, biotechnology, and medical device manufacturing, where contamination control is critical.
- Ease of Cleaning:Â They are easier to clean, making them suitable for applications where hygiene is paramount. The smooth, non-porous surfaces of the walls can be quickly and thoroughly sanitized, reducing the risk of contamination.
- Higher Static Pressure: Capable of maintaining higher levels of static pressure, they prevent particulate intrusion more effectively. This feature is essential for industries that require stringent contamination control.
- Environmental Control: They allow for precise control over humidity, temperature, and positive/negative pressure, making them ideal for applications requiring specific environmental conditions. This level of control is crucial for industries such as aerospace, semiconductor manufacturing, and high-tech research.
Detailed Comparison: Softwall vs. Hardwall Cleanrooms
Structure and Materials
- Softwall Cleanrooms: Constructed with flexible vinyl curtains, they offer a lightweight and portable solution. These curtains can be easily replaced or adjusted, providing flexibility in terms of size and configuration. Softwall cleanrooms typically have frames constructed from aluminum or stainless steel. These materials make the frames strong and simple to assemble and disassemble.
- Hardwall Cleanrooms: Hardwall cleanrooms utilize prefabricated wall panels made from materials such as steel, aluminum, or high-density polyethylene (HDPE). These panels are strong and long-lasting, able to handle high pressure and maintain control over the environment. The panels are designed to fit together seamlessly, ensuring an airtight and contamination-free environment.
Installation and Expansion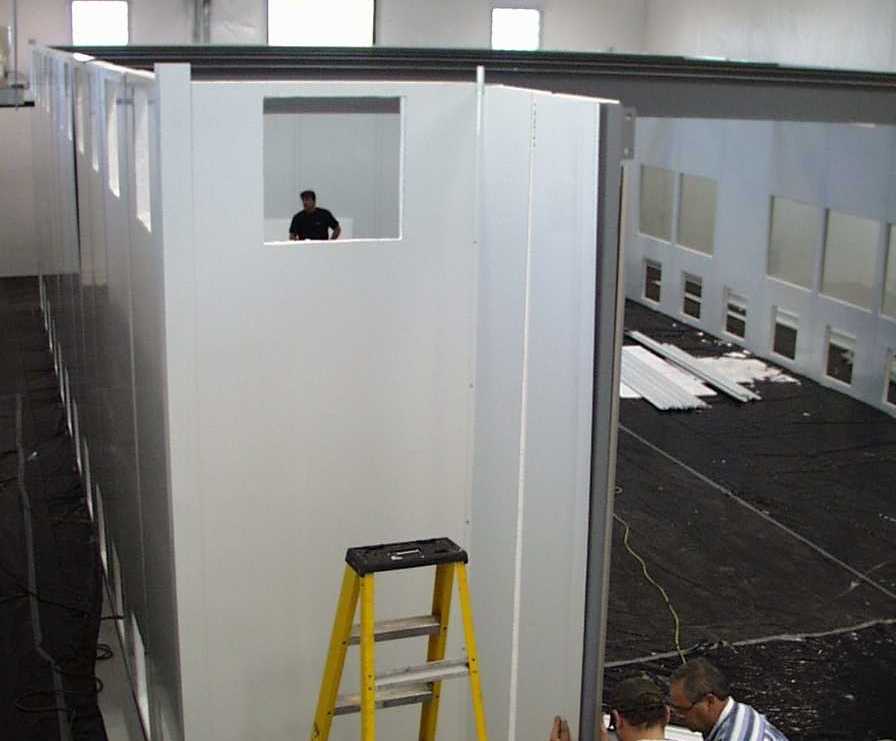
- Softwall Cleanrooms: Due to their lightweight and modular design, they can be installed quickly and with minimal disruption. This makes them ideal for temporary or rapidly changing needs. Additionally, they can be easily expanded or reconfigured as project requirements change, providing a flexible solution for dynamic industries.
- Hardwall Cleanrooms: Although hardwall cleanrooms take longer to install due to their more complex structure, they offer a more permanent solution. The installation process involves assembling the prefabricated wall panels and integrating the necessary HVAC and filtration systems. Once installed, they provide a stable and durable environment that can be maintained over the long term.
Cost Considerations
- Softwall Cleanrooms: Generally, softwall cleanrooms are more cost-effective than hardwall cleanrooms. Their lower material and installation costs make them a popular choice for projects with tight budgets. Additionally, the ability to quickly expand or reconfigure them can result in cost savings over time, particularly for projects with changing requirements.
- Hardwall Cleanrooms: While the initial cost of hardwall cleanrooms is higher due to the use of more durable materials and a more complex installation process, they can offer long-term cost benefits. They are more effective at preventing contaminants from entering and have a longer lifespan. This can lead to cost savings on maintenance and make them a valuable investment for critical applications.
Deciding Between Hardwall and Softwall Cleanrooms
When deciding whether to use a softwall or hardwall cleanroom, consider the following factors:
- Application Requirements: Assess the specific needs of your project, including the level of cleanliness required, the type of contaminants to control, and the environmental conditions to maintain. Decide if you need the strict control of hardwall cleanrooms or the flexibility of softwall cleanrooms for your application.
- Budget: Determine your budget constraints and evaluate the cost-effectiveness of each type. Softwall cleanrooms tend to be more affordable and quicker to construct, while hardwall cleanrooms offer superior durability and control.
- Future Expansion: If you anticipate the need for future expansion, softwall cleanrooms provide a flexible solution that can be easily modified. In contrast, hardwall cleanrooms offer a more permanent, robust structure.
Case Studies
Pharmaceutical Manufacturing and Biotechnology Research
A leading pharmaceutical and a biotechnology research lab both required cleanrooms for sensitive applications. The pharmaceutical company chose a hardwall cleanroom to maintain high levels of static pressure and environmental control, ensuring uncontaminated drug formulations and successful regulatory compliance. Similarly, the biotechnology lab selected a hardwall cleanroom for precise control over temperature, humidity, and particulate levels, essential for accurate genetic testing and analysis.
Aerospace Component Manufacturing
An aerospace company needed a cleanroom to manufacture and assemble critical aircraft components. Due to the stringent contamination control requirements and the need for precise environmental control, the company selected a hardwall cleanroom. It maintains high static pressure and effectively controls humidity and temperature. This ensures that the components produced meet high-quality standards.
Electronics Assembly
An electronics manufacturing company needed a cleanroom to assemble sensitive electronic components. They opted for a softwall cleanroom due to its flexibility and rapid deployment capabilities. The one provided an effective barrier against dust and contaminants, allowing the company to meet its production deadlines and maintain product quality.
Conclusion
Understanding the differences between hardwall and softwall cleanrooms is essential for selecting the right solution for your controlled environment needs. At Modular Cleanrooms, our expert team is here to guide you through the process, ensuring yours is designed, constructed, and optimized to meet your specific requirements.
Contact us to start your project today. Our specialized staff will ensure that yours operates to your exact needs, providing a customized solution that aligns with your project goals and industry standards. With our expertise and commitment to quality, you can trust us to deliver the ideal solution for your application.
By carefully considering your project requirements, budget, and future needs, you can make an informed decision on whether a softwall or hardwall cleanroom is the best fit for your application. Our team is dedicated to assisting you in achieving your goals. We provide expert guidance and support every step of the way. Whether you need a flexible, cost-effective solution or a robust, high-performance cleanroom, we have the expertise and resources to meet your needs.